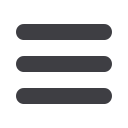
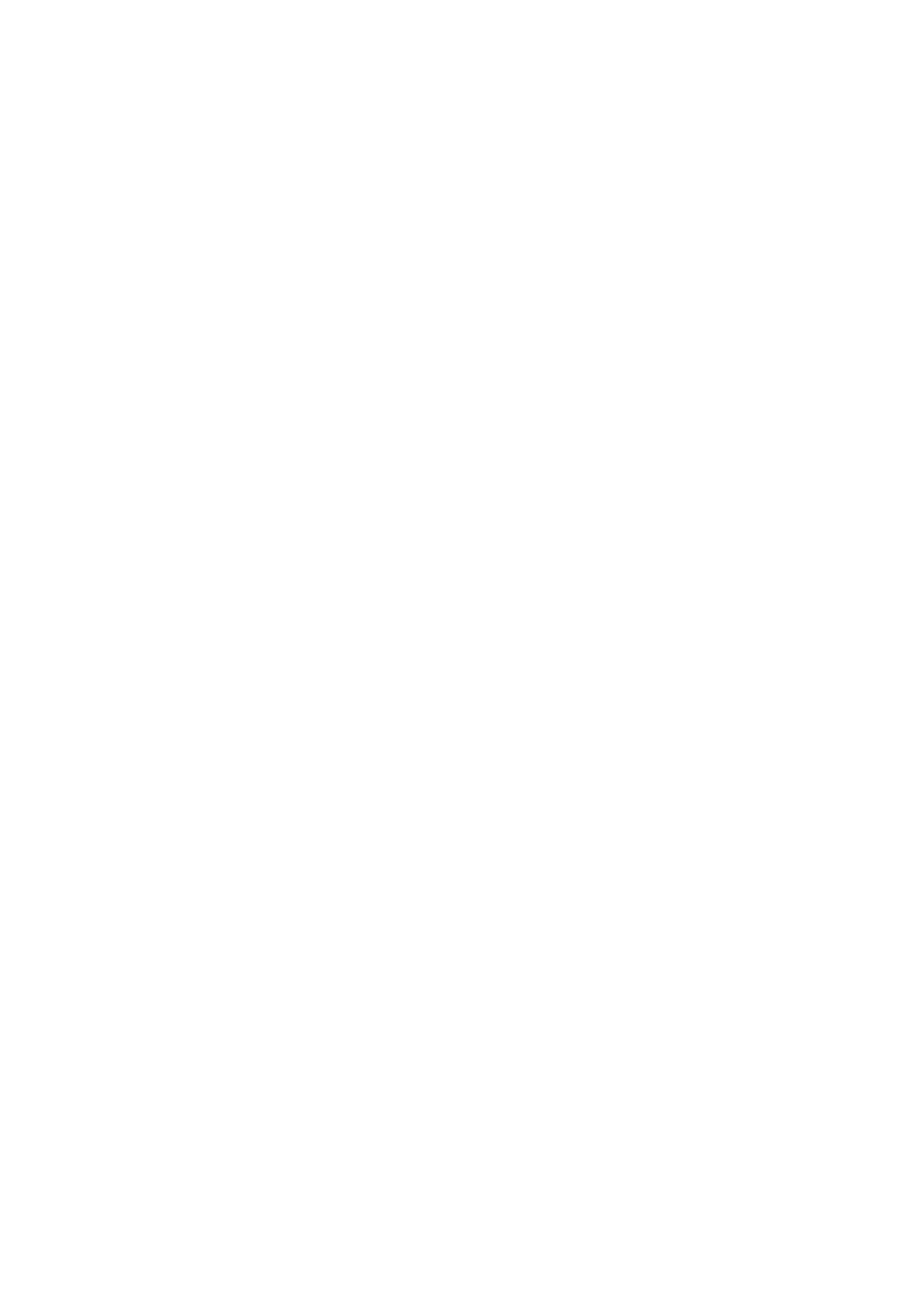
Prysmian Group – 2015 Sustainability Report
Environment
________________________________________________________________________________________________
125
At the Calais factory, France, the consumption of water per km of product was reduced by 36% in 2015
compared with 2014. This was primarily achieved by improved supervision of the functioning of the technical
plant and better preventive maintenance of key plant equipment (filters, pumps etc.), but also by keeping a
daily record to monitor water consumption.
At the Nurnberg factory, Germany, electricity consumption per tonne of product fell by 19% in 2015
compared with the previous year. This was made possible by replacing the dryers and reducing the losses
from the compressed air system.
The use of a new type of ink that fixes better at the Washington factory, United Kingdom, reduced the need
to clean with solvents and the consequent dispose of them, thus cutting by 76% the quantity of waste
solvents compared with the previous year.
Telecom operating unit at the Slatina factory, Romania, also benefited from the drastic reduction in
packaging sent for disposal observed at Energy unit.
Optical Fibre
In 2015, at the Eindhoven factory, the Netherlands, there was a marked increase in the quantity of
germanium-based waste sent for recycling. The recycling of this chemical element commenced in 2009, as a
result of combined efforts with the local supplier of raw materials and vegetable fibre.
This action is particularly meaningful, since germanium is a precious substance and its recycling therefore
falls within the factory's sustainability programme.
Additionally, two new operational flows have increased by almost 40% the volume of germanium recycled:
the first flow consists of scrapped fibres that are processed in order to extract the germanium; the second
flow, on the other hand, uses the PCVD (Plasma Chemical Vapour Deposition) process to separate a
substance that is collected in order for the germanium to be recovered at the premises of our suppliers.
The recycling yield from these two flows is expected to improve further, and another flow will be explored in
the near future.
At the same location, 25,713 kg of optical fiber on bobbins were sent for recycling in 2015.