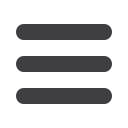
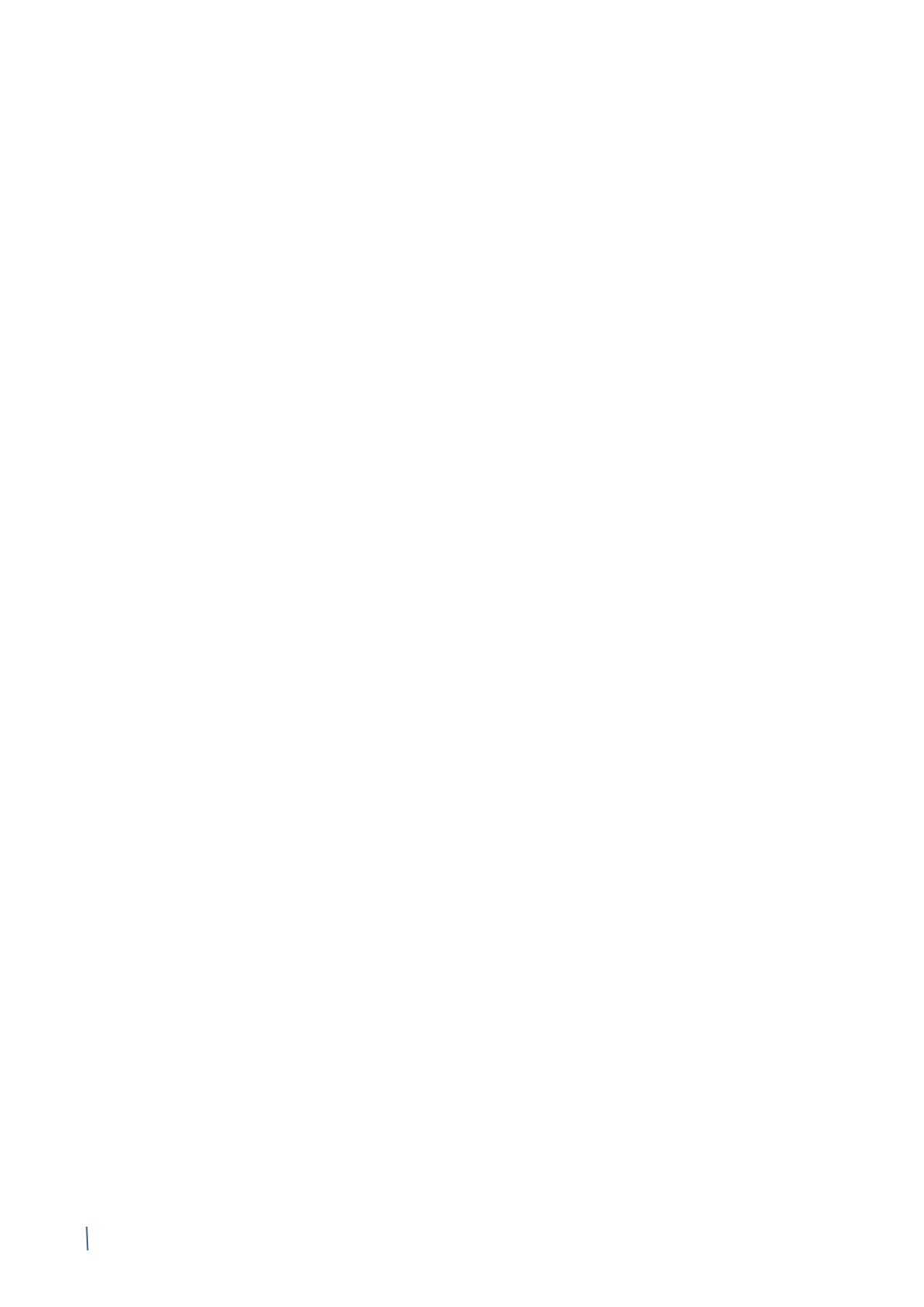
Consolidated Financial Report |
DIRECTORS’ REPORT
2014 Annual Report
Prysmian Group
106
conductor, featuring a weight-optimised conductor
and a copper-wire screen with copper laminated foil,
specially designed for the American market. EHV product
development also saw the start of a major project to
develop the HVDC 525 kV system with extruded XLPE
insulated cables and related accessories. This project,
also intended for the production of submarine cables,
includes several alternative solutions in terms of both
cables and accessories, in order to meet every possible
customer requirement. The high voltage underground
cables area reported the development of an aluminium
wire screen with protective aluminium laminated foil,
allowing a cost saving of up to 15% compared with
the corresponding copper wire screen solution with
aluminium laminated foil. Lastly, work continued on
starting up and qualifying the Rybinsk plant in Russia:
in fact, 110 kV qualification was achieved and the 330
kV prototype with a Milliken 2500 mm² aluminium
conductor was produced for the subsequent phases of
testing.
• With reference to developments in P-Laser technology,
the 150 kV class passed its qualification test; the test,
conducted on a system complete with accessories
(joints and terminations), was completed with a series
of additional high-temperature high-voltage tests. In
view of the promising results obtained during internal
prequalification testing conducted in 2013, qualification
testing started for a P-Laser HVDC 320 kV cable and
related accessories. The P-Laser system is particularly
suitable for high voltage direct current (HVDC) appli-
cations because of the greater chemical stability of
its insulating material for which no kind of treatment
(degassing) before commissioning is required.
• The Oil & Gas cables business reported continued
product development and related technology transfer
between Group factories. In particular, to meet the needs
of our customers in the global change of the business
(increased production from new offshore platforms
in China and Brazil), technology and know-how for
offshore NEK606 compliant cables were transferred to
the Chinese plant in Tianjin, with related training of its
technical staff and preparation of appropriate manuals
in English and Chinese; during the year similar activities
were also carried out at the Suzhou plant. In terms of
products, new solutions were developed for harsh envi-
ronmental conditions and to allow vital communication
by emergency systems even in extreme conditions. The
Drilling Package, a complete cabling solution for Oil &
Gas drilling applications both onshore and offshore, was
also launched globally.
• With regard to the development of Prycam technology,
two important new innovations were developed in 2014.
These included the Prycam DLoG, a digital data logger
with 4 analogue inputs and 4 totally configurable digital
inputs to accept temperature, pressure, current, voltage
sensors, and so on; this device is designed to monitor
electrical parameters in fixed installations and, like
other members of the Prycam family, it allows users to
see data acquired wirelessly and to send that data to the
common Pry-Mon monitoring platform. The Pry-Mon
platform was enhanced to accept data from Prycam
Portable, from Prycam Grids and from DTS systems. The
second innovation in the family was the new Prycam
Wings sensor. Developed using the experience of the
Prycam Portable sensor to measure partial discharges,
Prycam Wings also includes temperature and current
sensoring.
Achievements in the Telecom operating segment included:
• In the optical fibre field, several of the Group's factories
were got ready for full production of bend-resistant
BendBrightxs fibres, which have much better micro
and macro-bending performances than competitor
products. A number of improvements were also made
at several factories to secure a significant reduction in
fibre production costs. In the area of multimode fibre,
WideCAP OM4 was launched, a new fibre capable of
40Gb bidirectional transmission with two channels at
850 and 900nm, and potential upgrade to 4 * 25Gb to
meet the future needs of the 100Gb superfast network.
• In the optical cables field, the Flextube family of cables
was enlarged with the addition of a record density
product containing 4.2 fibres per mm² in a 1728 fibre 23
mm diameter cable, made using fibres measuring 200
micrometres in diameter. These products represent an
excellent solution for use in conduits congested with
other cables. Dry/dry technology was also developed
for Flextube cables in order to reduce cable installation
time even further and so reduce overall installation
costs. At the Slatina plant in Romania, now one of the
major European centres of optical cable production,
investments continued for a significant increase in
production capacity of the Flextube and Drop cables. In