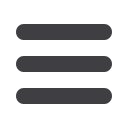
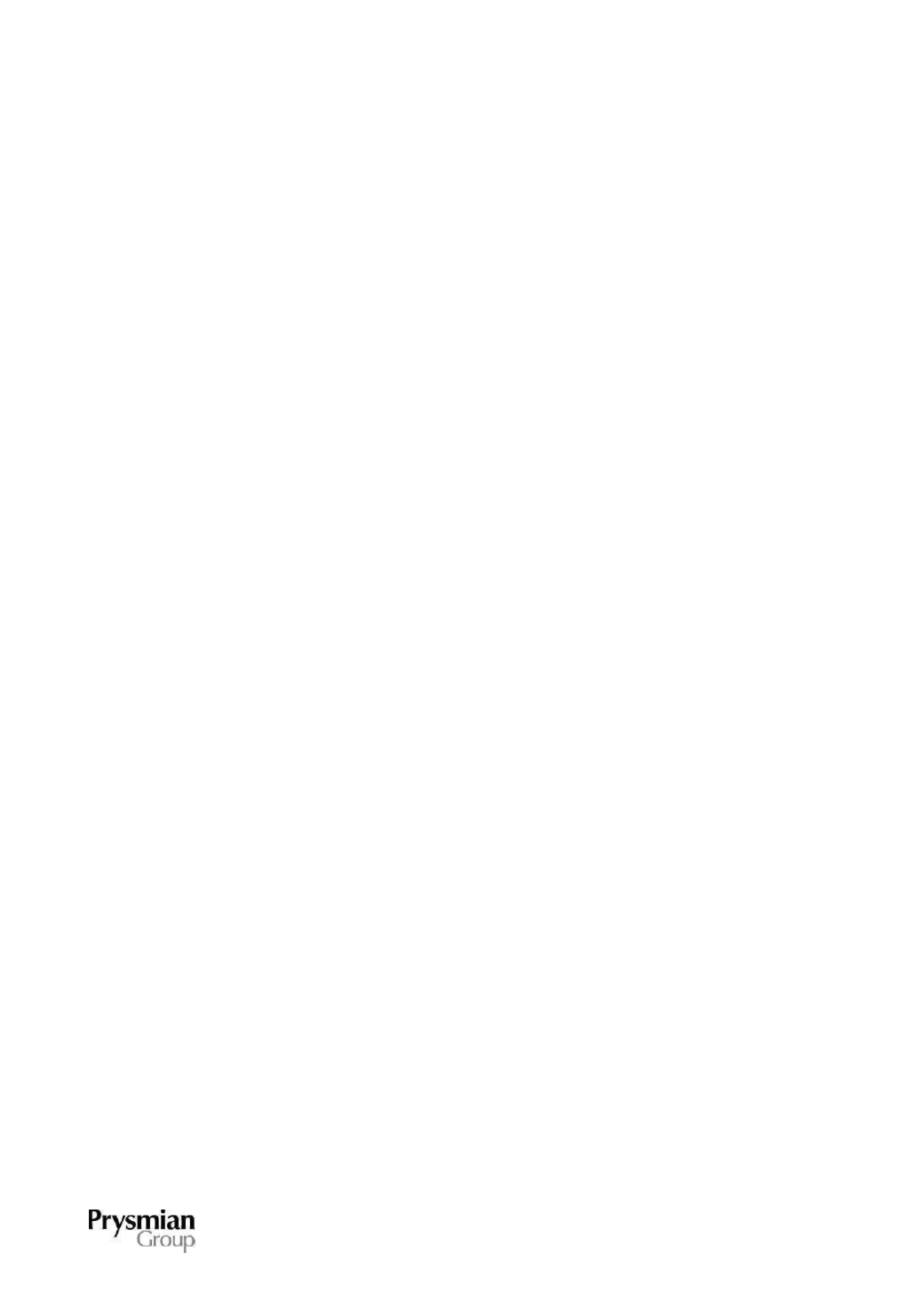
PRYSMIAN GROUP | DIRECTORS’ REPORT
114
cables in the armouring, were designed and qualified. New techniques of conductor diameter jointing were
developed to collect large aluminium conductors together in conductor platforms and to join conductors of
different cross-sections and materials. These technologies can be applied to both AC cables and direct
current (DC) cables and allow a more efficient system design and significant reduction in costs. The first
prototype with alternative armouring serving the development of cables for installation at great depths
underwent full mechanical testing, while a second prototype was designed for installation at depths of more
than 2,500 metres. The latter prototype will use non-metallic reinforcing elements that were optimised and
developed during the year. In the area of MI cables (Mass Impregnated paper-insulated), work continued to
improve the recovery plan for the WesternLink project and its 600 kV HVDC cables insulated using PPL
technology, and research began into alternative materials and into optimising the design and manufacturing
process to achieve a significant increase in operating voltage compared with the current level of 600 kV.
With reference to the 525 kV extruded cable project, work on developing a flexible coupling point reported its
first positive results.
Extra High Voltage (EHV) Underground Systems.
In the field of product development of EHV underground
cables, development and type tests were completed for the new 525 kV HVDC system and certified
according to CIGRE TB496. This important achievement is a milestone for cable power transmission,
allowing a single circuit to carry over 2.6 GW in power, according to the type of installation, which is more
than twice as much as can be carried by 320 kV systems currently in service. The Prysmian Group's know-
how in materials, technology and electrical testing has been decisive in achieving this result. HVDC systems
are the preferred choice for carrying high voltage power over long distances via insulated cable. Prysmian
precedents in the field of HVDC transmission using extruded cables include submarine interconnectors like
the 200 kV Transbay cable, the 320 kV power lines in the North Sea and the 320 kV underground
interconnectors between France and Spain, and between France and Italy. The EHVDC project will continue
with the development of a totally new system comprising solid-insulated cable and pre-printed accessories,
as well as the development of non-conventional jointing technology. Also in the area of EHV product
development, three extruded cable prototypes were completed with Milliken copper conductors with 2500
and 3500 mm² cross sections and a longitudinally welded aluminium sheath. The two 2500 mm² prototypes
have been insulated with alternative materials to those currently in use. The test circuits have been mounted
at the IPH laboratories (CESI) in Berlin and the qualification tests according to the IEC62067 standard are in
the process of being initiated. Development of EHV cables with large cross-section aluminium conductors
(3000 and 3500 mm²) was also completed and the prototypes are now undergoing official qualification tests
according to the IEC62067 standard. Optical fibre has been inserted in these prototypes, with longitudinally
welded aluminium sheaths, for on-line measurement of cable operating temperature.
Technology Development and Transfer
.
In the area of technology development and improvement, a project
is in progress to optimise medium and high voltage conductors, by reducing cable weight and diameter in
accordance with regulatory requirements for direct current resistance. Weight savings of around 2-3% have
been achieved for the conductor cross-sections modified to date. Still in this area, some new large cross-