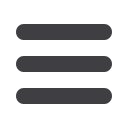
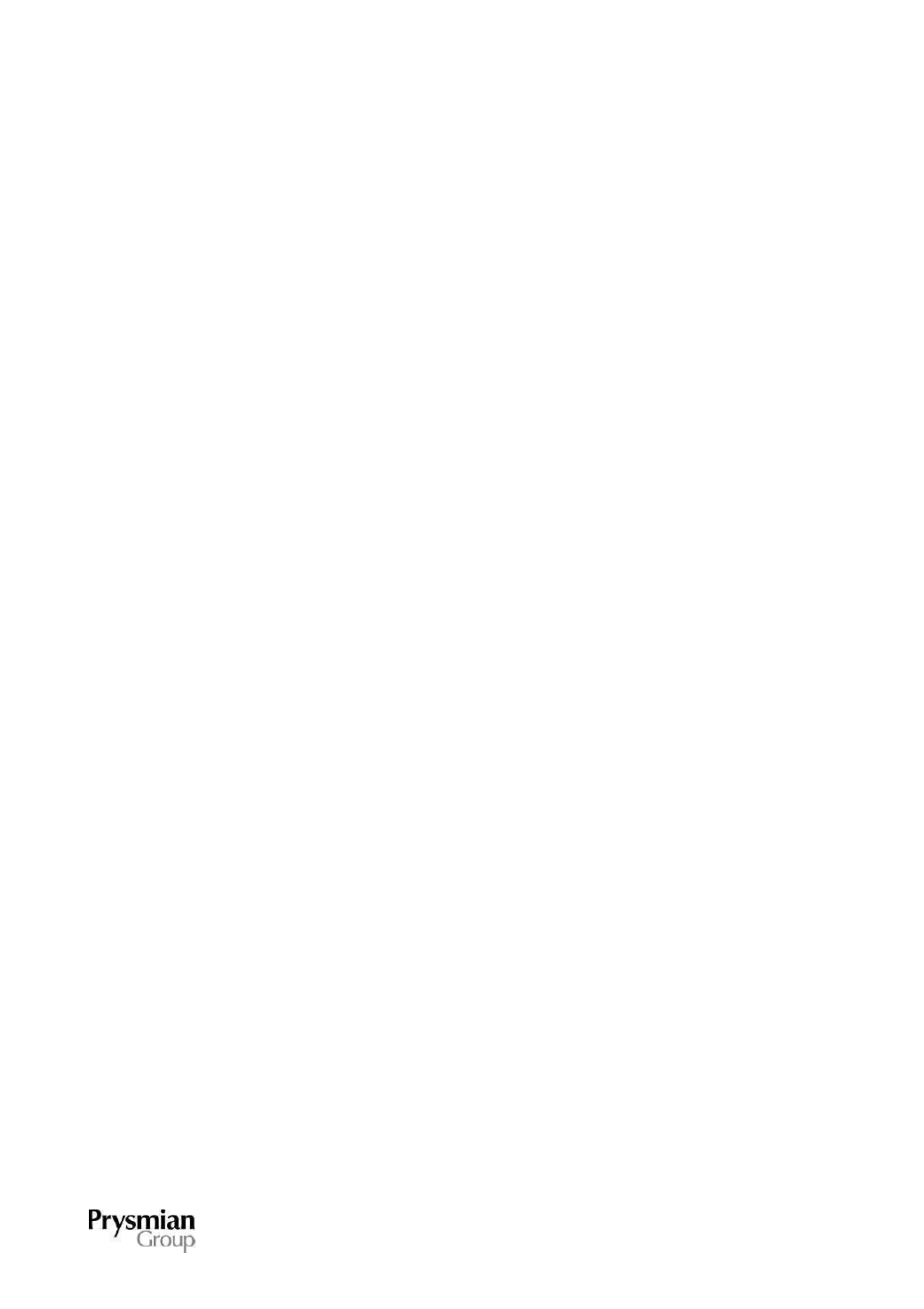
PRYSMIAN GROUP | DIRECTORS’ REPORT
115
section Milliken copper conductors have been developed with an improved AC resistance coefficient thanks
to a reduction in the "skin effect", achieved by same-direction stranding of the sectors and oxidation of the
wires.
With reference to technology transfer, prototype EHV cables went into production at the Rybinsk plant
(Russia) with the manufacture of 330 kV 2500 mm² copper cables, while industrial production started for 110
kV 1200 mm² and 1600 mm² copper cable. Work continued on starting up and qualifying the factory in
Slatina (Romania) for the production of 110 kV 630 mm² copper prototypes and 150 kV 1000 mm² aluminium
prototypes. Qualification tests according to VDE standards are in progress for the first prototype and
according to IEC standards for the second. The VCV2 line at the Abbeville plant started operating with the
production of two 245 kV 2500 mm² copper prototypes. The type tests are in progress. The HV business unit
started a Best Practices HV project to share, through technical visits and technological assistance, the best
practices used by the Group for selecting raw materials, design and technology.
As regards technology transfer involving special and low voltage cables, NEK606 technology was
successfully transferred to operating companies in China and Brazil, while work was started on the project to
standardise raw materials and technologies. LSOH (Low Smoke Zero Halogen) technology was upgraded at
the plants in Melaka (Malaysia) and Schwerin (Germany).
P-Laser Technology
.
Development of Energy cable P-Laser technology has continued with particular
intensity for HVDC applications; the thermoplastic nature of P-Laser insulation significantly improves
performance by such applications thanks to greater chemical stability and the absence in HPTE (High-
performance Polypropylene Thermoplastic Elastomers) insulation of cross-linking by-products. The 320 kV
DC system successfully completed its qualification process. The complete loop of terminals and joints for
underground installation passed pre-qualification tests according to the requirements of CIGRE TB 496 for
VSC systems with a 90°C conductor temperature, 20°C above the temperature at which standard XLPE
(Cross-Linked Poly-Ethylene) insulated systems are normally qualified. Furthermore, the same cable was
subjected to a narrow but particularly significant series of tests (defined with an important TSO that operates
in the HVDC field), designed to evaluate the system at a 350 kV voltage with polarity reversals, typical of
LCC systems. The tests, conducted in this case at a conductor temperature of 70°C, demonstrated the
HPTE insulated system's excellent performance even with rapid polarity reversals, when the system is
required to rapidly remove the locally accumulated space charges; this situation is considered to be
particularly critical for standard XLPE insulated systems, given the presence of the cross-linking by-products
that act as traps for the space charges. Based on the promising results described above, work has started
on developing and applying P-Laser materials to the 525 kV load class, which will be the next technological
frontier for long distance DC connections. With reference to distribution systems, P-Laser cable has been
qualified for certain utilities operating in Northern Europe (Finland), a region in which overhead lines are
actively being replaced with buried lines. The superior performance of the P-Laser system in terms of
reliability and thermal rating, allow local operators to significantly improve the quality of service provided. The
P-Laser cable design for application in Finland has been adapted to the requirements of local utilities, in
particular its defensive properties against the passage of water through the cable's various constituent parts.