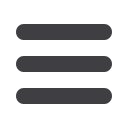
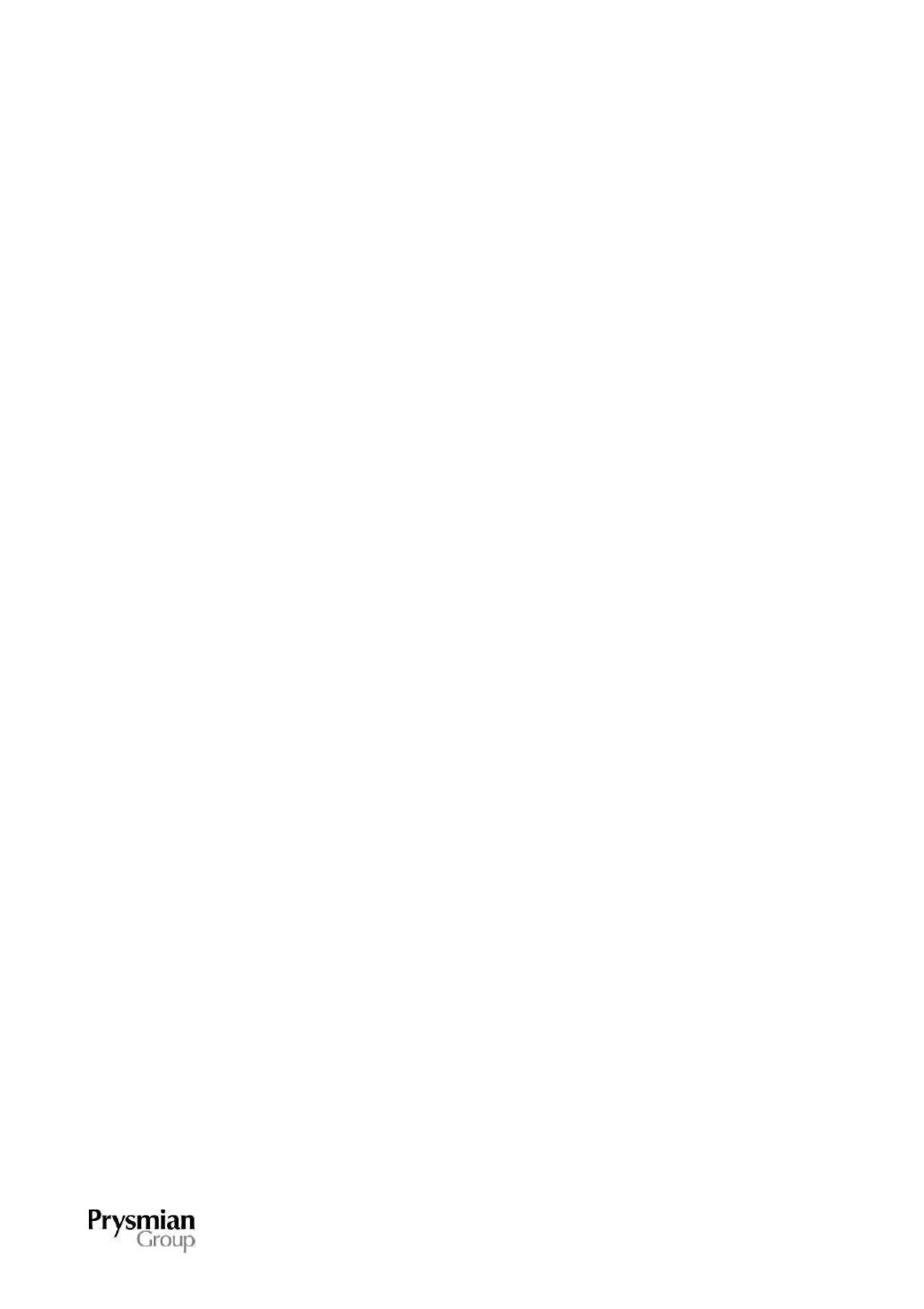
PRYSMIAN GROUP | DIRECTORS’ REPORT
122
AN INTEGRATED SUPPLY CHAIN
SOURCING
Once again in 2015, the Prysmian Group was able to deal with fluctuations in base metal prices through
strict application of its hedging policies and daily matching between purchase and sales commitments.
The main raw materials used by the Group in its production processes are copper, aluminium, lead, special
glass and coating for optical fibres, as well as various petroleum derivatives, such as PVC and polyethylene.
In a market characterised by continued global economic fragility with only a slight recovery in volumes,
average prices of the principal plastic raw materials reported fluctuating trends during 2015 and were
generally lower than the year before. In the case of base metals, copper, aluminium and lead prices were
significantly lower than the year before, down 20% in USD (2015 average vs 2014 average), reflecting
persistent stagnation in some West European countries, compounded by another slowdown in emerging
economies (China and Brazil) raising fears about possible reductions in future demand by these countries.
The strengthening of the US dollar caused the euro prices of these metals to post a more moderate
reduction (-4%) in the case of copper, but increases of 2.1% and 6.4% for aluminium and lead respectively.
The Brent crude price closed the month of December 38% lower year-on-year, confirming the downward
trend in prices since August 2014. Ethylene prices also reported a steep drop. Among the ethylene
derivatives, polyethylene resins generally posted an increase, which was higher for the linear type due to a
product shortage arising from unplanned downtime in European ethylene and polyethylene production
facilities, and from lower imports of this material from dollar-zone countries. The price of PVC resins was
essentially stable; plasticiser prices were significantly lower, reflecting trends in the related raw material costs
and persistently weak demand in the construction industry.
Once again in 2015, the Prysmian Group was able to deal with fluctuations in base metal prices through
strict application of its hedging policies and daily matching between purchase and sales commitments. Sales
price adjustment mechanisms, combined with judicious hedging, helped in fact to mitigate the impact of price
fluctuations on the income statement. As for other raw materials, work continued to rationalise and
consolidate the supplier base, using all the synergy and volume levers offered by the Group's size. Risk
management activities also continued with regard to the supplier portfolio, aimed not only at reducing
dependence on individual suppliers, but also at strengthening partnerships with core suppliers or suppliers of
critical technologies. The added strengthening of commercial relationships with core suppliers over the year
allowed the Group to minimise costs and the risk of disruption in supplies, ensuring benefits not only in the
short term but also in the medium and long term.
Copper
The average cash settlement price per tonne of copper on the London Metal Exchange (LME) was USD
5,502 (Euro 4,948) in 2015, representing a 19.8% decline on the prior year average price in USD (USD
6,860 per tonne) and a 4% decline in EUR (Euro 5,167 in 2014). Fluctuating between a low of USD 4,515