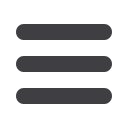
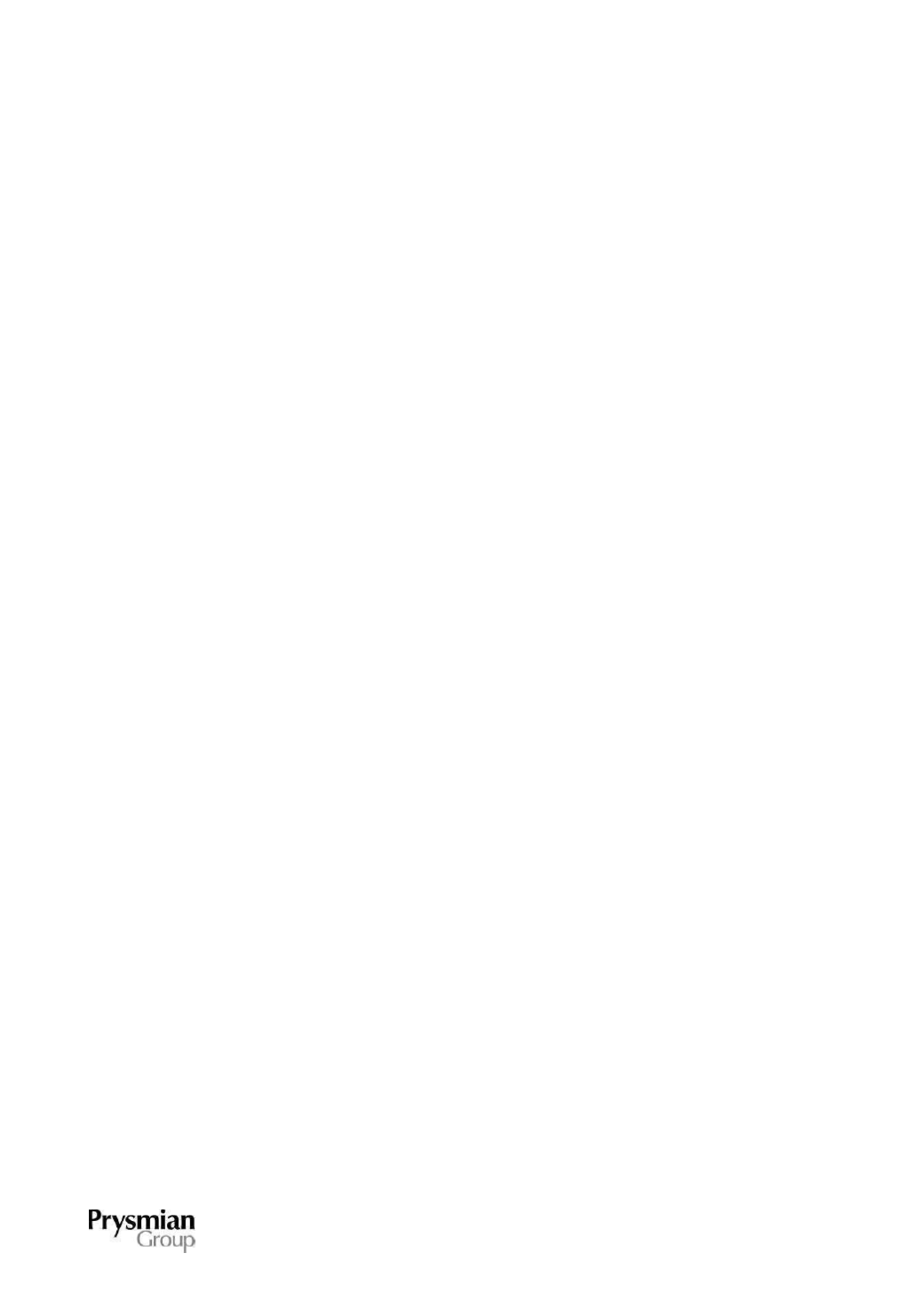
PRYSMIAN GROUP | DIRECTORS’ REPORT
127
Melaka plant was expanded in order to produce instrumentation and control cables for the Far East market.
Lastly, in Hungary, the Kistelek plant is about to complete two projects: the first for a production line for
rubber cables serving the Central European market, the second for the expansion of production capacity of
Trade & Installer cables, again to serve the Central European market but from a source with lower
processing costs.
Telecom
. The Telecom operating segment saw a continuation of the major investment in the Sorocaba plant
in Brazil for verticalisation of the optical fibre production process in order to serve the South American market
and particularly the Brazilian one; it was also decided to invest in creating a verticalised plant in North
America, with Claremont in the United States the plant selected for this project. There was also continued
investment to increase optical cable production capacity at the factory in Slatina (Romania), where work also
started to build a new plant entirely devoted to Telecom cables, as further proof of the intention of creating
one of Europe's centres of excellence for optical telecom cables.
Efficiency
. Capital expenditure on achieving efficiencies to reduce fixed and variable costs, particularly in
relation to materials usage and product design, accounted for approximately 31% of the total. In particular,
the Energy Products segment made significant investments in efficiency, particularly in the metallurgical area,
following the Group's decision to complete the process of vertical production at some of its plants (Schuylkill
Haven and Abbeville in North America, and Suzhou in China). The Telecom segment's European optical
fibre manufacturing facilities in Battipaglia (Italy) and Douvrin (France) continued to invest in efficiency for the
purpose of significantly reducing fibre manufacturing cost. In particular, the Italian plant completed both the
construction of a trigeneration plant that will reduce its energy costs and the project to increase the size of
preforms. Lastly, in Tunisia, it was decided to expand the existing plant that makes kits for cables serving the
connectivity sector, with the intention of bringing in-house work formerly done by outside companies.
IT, R&D
. Some 5% of capital expenditure was devoted to the ongoing upgrade and development of
information systems and to research and development (the portion of expenditure not expensed to income).
In particular, there was continued spending on rolling out the "SAP Consolidation" project, aimed at
standardising the information system in all the Group's operations over the next few years: in 2015, the
kernel of the new ERP system was upgraded and the system was rolled out to Britain and Brazil.
Base-load.
Capital expenditure on structural maintenance work accounted for about 10% of the total, in line
with previous years.
Other.
This category (accounting for 10% of total expenditure) mainly refers to the start of work at the
Ansaldo 20 industrial site, in the Bicocca district of Milan, on building the Group's new headquarters, which
will extend over an area of more than 20,000 m
2
and allow the Group to consolidate all its Milan-based
company functions in one place, with a resulting saving in running costs.