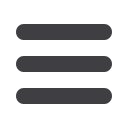
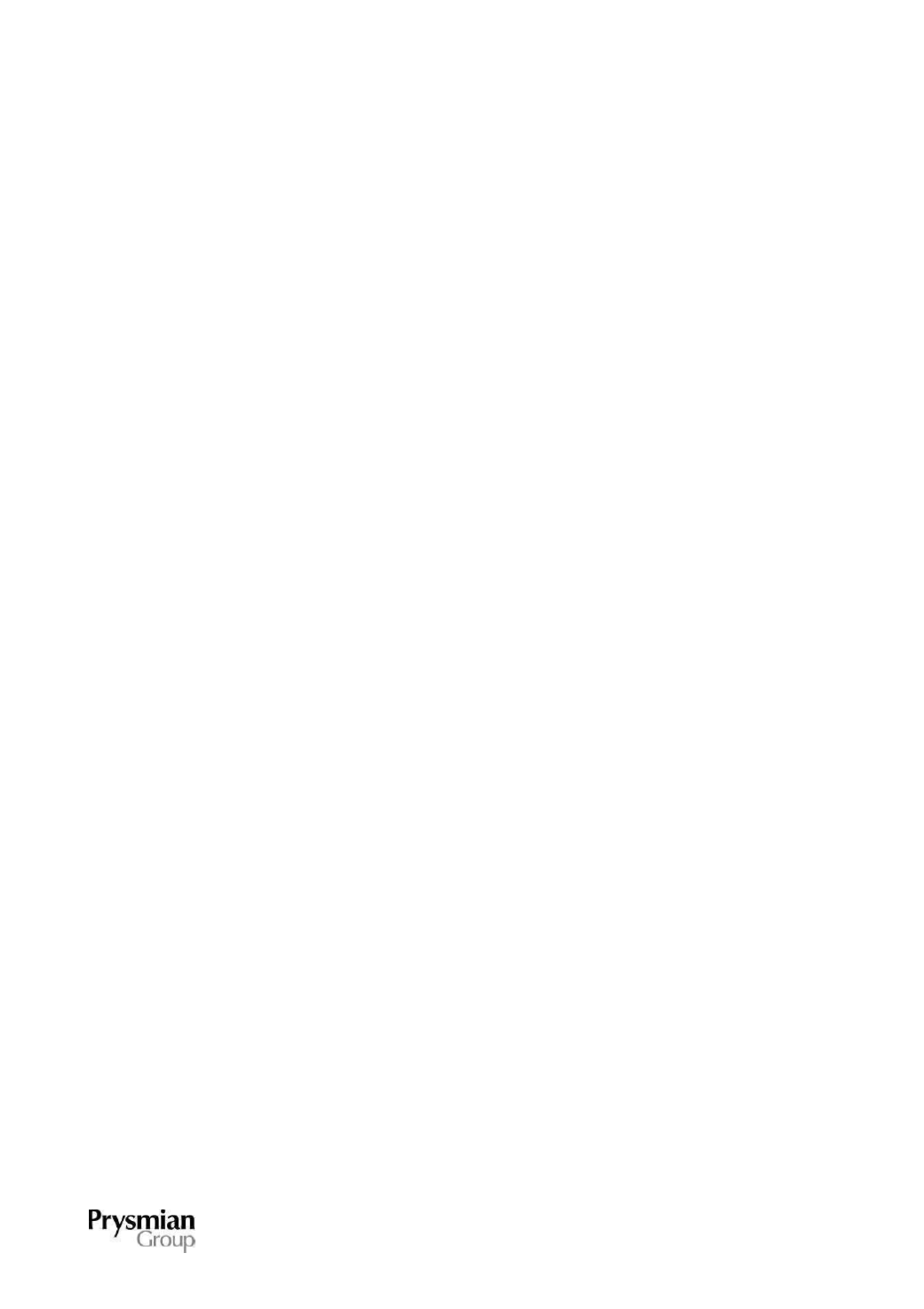
PRYSMIAN GROUP | DIRECTORS’ REPORT
130
LOGISTICS
Prysmian Group strengthened its strategic focus on Customer Centricity in 2015, confirming the improving
trend of recent years in customer service.
The year also saw good results in terms of inventory management, with a positive impact on cash flows.
The Logistics function manages all the Group's intercompany flows at the level of both annual budget and
monthly operations, with the aim of satisfying demand in all markets without a local production source due to
lack of capability or production capacity. The Logistics function also manages short and medium-term
production allocations and planning through Sales & Operations Planning (S&OP), a process which serves
as the link between the demand cycle (sales) and the supply cycle (manufacturing and procurement). The
Group plans production according to whether a product is classified as:
Engineer to Order
: mainly used in the Energy Projects segment for Submarine, High Voltage and Umbilical
cables, businesses in which the Prysmian Group supports its customers right from system design all the way
through to final cable laying.
Assembly to Order
: this approach allows a fast response to demand for items that use standard components
but differ only at the final stages of production or packaging. This approach has the dual objective of
responding rapidly to market demand while at the same time keeping inventories of finished goods to a
minimum.
Make to Order
: in this case, production is activated and goods shipped only after receipt of a customer order,
significantly reducing unused inventory levels and the time that raw materials and finished goods remain in
stock.
Make to Stock
: in contrast, under the MTS approach, generally used for more standardised products,
inventory management focuses on producing items for stock to allow a fast response to demand. This model
is mainly applied in the Energy Products and Telecom operating segments.
In keeping with the Group's strategic objectives and as part of the Customer Centricity and Factory Reliability
initiatives, Prysmian Group continued in 2015 with the actions already started in recent years to improve
logistics services, in terms of lead-time flexibility, timeliness and efficiency.
The punctuality and reliability of its processes have confirmed the Prysmian Group's strong focus on
continuous improvement. The On Time Delivery (OTD) statistics, measuring the ability to serve the customer
by the delivery date agreed at the time of confirming order receipt, continued to improve in 2015 in both the
Energy Products and Telecom operating segments, as shown in the following graphs.
Besides the absolute increase in the level of On Time Delivery, 2015 saw another decrease in the proportion
of plants performing below the 90% mark, thus reflecting more consistent performance between the Group's
various plants.