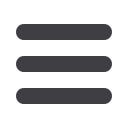
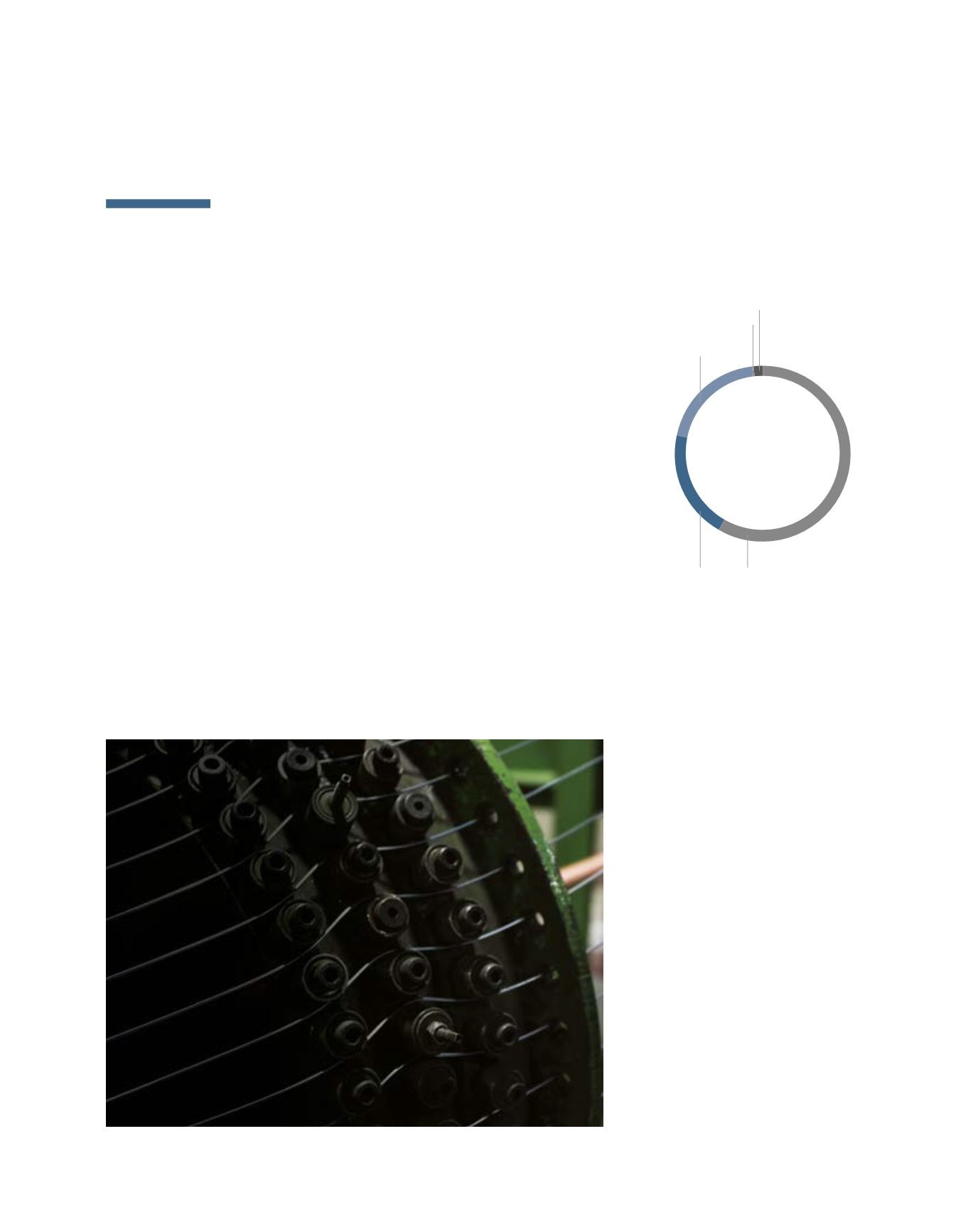
5.
EFFICIENCY CONTINUOUSLY INCREASING
PRYSMIAN GROUP
2015
YEARLY OVERVIEW
Implementation of the “factory reliability”
concept, introduced in 2010, enabled yet
more improvements in 2015 in the quality
of the planning and supply processes in
terms of controlling volumes and inventory
levels. Group suppliers source the main
raw materials used by Prysmian: copper,
aluminium,
lead,
various
petroleum
derivatives (such as PVC and polyethylene),
components for power and telecom cable
accessories, as well as special types of glass
and sheathing for optical fibre.
The strategic approach to supply chain
management is based on five priorities
that also include environmental and social
objectives.
A SUPPLY CHAIN DESIGNED FOR THE CUSTOMER
Metals, particularly copper and aluminium,
are a key resource for Prysmian’s production
processes: in fact, they account for around
70% of the raw materials used. Prysmian
purchases copper and aluminium wire rod
from the world’s leading manufacturers
and only in special cases does it produce
its own copper rod, the volume of which is
nonetheless less than 10% of the total.
Also in the case of aluminium, the Group
has decided to concentrate increasingly on
suppliers that are vertically integratedunder a
strategy that assures the security of supplies
while also having cost and environmental
benefits thanks to simplification of the
logistics and elimination of the ingot re-
smelting cycle.
The Group absorbs slightly more than 2% of
the world’s copper production and about 5%
of the copper used globally in the electrical
and electronic sector, representing one of
this market’s leading economic players.
The procurement strategy follows two
directions: firstly, procurement from
producers that are as integrated as possible
with the ability to guarantee long-term
supplies; secondly, procurement from all
major global producers, in order to ensure
efficient coverage of requirements and
optimise the metals logistics chain.
The Group has developed genuine
partnerships with the integrated suppliers,
while also entering into short-term
agreements with non-integrated suppliers
to assure the necessary flexibility.
Total raw material purchases amounted to 1,155
ktonnes in 2015, of which 59% represented by
metals, consistent with the prior year figures.
Once again this year, 11% of the raw materials
used were sourced from recycled materials.
Metals, key resource to manage
Aluminium: simplification
of logistics
Copper: a major global player
RAW MATERIALS PURCHASED
BY THE GROUP IN 2015 (KTONNE)
Customer service continued to be
a focal point during 2015, under the policy
adopted in prior years with the objective
of improving flexibility, reliability
and time to market.
• ALWAYS AND ONLY USE QUALIFIED SUPPLIERS
• ONLY USE MATERIALS WITH APPROVED TECHNICAL
CHARACTERISTICS
• GUARANTEE CONTINUITY OF COMMODITY SUPPLY AND
AVAILABILITY OF REQUIRED VOLUMES
• GUARANTEE ON-TIME DELIVERY AND HIGH QUALITY
STANDARDS OVER TIME
• ENSURE COMPETITIVE PRICES
Chemical products
0.4%
Metals
58.4%
Ingredients
19.7%
Compounds
20%
Other (paper,
yarns, tape, oil)
1.5%