Prysmian Ecoslim cable concept makes fibre network construction more sustainable
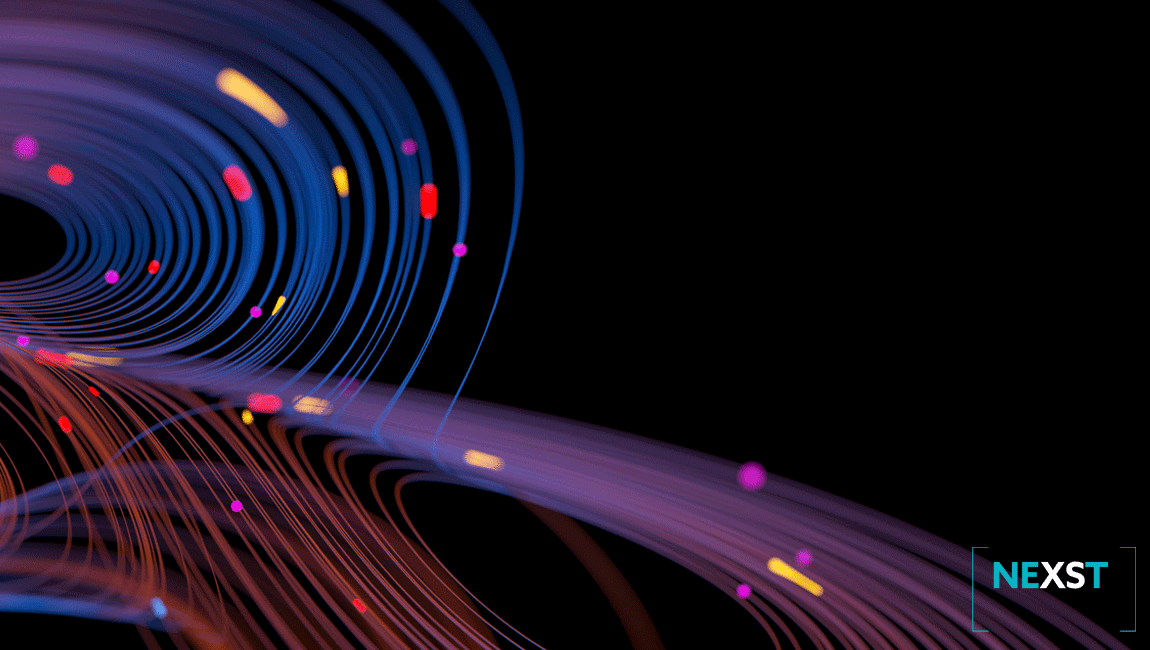
Thanks to the new Prysmian Ecoslim concept, customers can optimise the building of fibre networks at various points and realise more connections per year. The same capacity can be provided with significantly less waste. Compared to conventional cabling some 50% less raw material (plastic or PE) is required for the production of the new cables and ducts.
Ecoslim cables and ducts can be applied within existing Programmes of Requirements during the design phase, without requiring any changes or additional design costs. Sleeves are manufactured almost entirely (90%) from high-quality recycled PE, reducing CO2 emissions and waste.
Additional carbon reduction is achieved through savings in logistics, storage and packaging materials, as far greater lengths fit on each reel. As the smaller cables fit better in the existing ducts, fewer roadworks are needed. Less excavation work is also needed at concentration points in the network, which means less sand needs to be removed and treated. Polluted sands needs to be technically cleaned before it’s placed back. Obviously, digging up less sand means less energy is needed for transport and cleaning.
"The smaller and more flexible cables and tubes reduce the strain on the often-full cable routes," says Erik van den Oever Prysmian Group’s Commercial director Telecom Benelux. "In addition, they are easier to install, and spare tubes can be reused. Stripping and splicing take no longer than with ‘regular’ cable. During digging, these newer cables should also be less prone to damage than existing cable, as there’s more room around the fibres. What’s more, on a conventional 700 metre cable drum, the last 70 metres remain unused, as transporting this remainder is not cost-effective. However, as the new cables drums hold 1700 metres, that remainder is no longer 10% but around 3%.”
Following the development phase, the Ecoslim concept was tested in a greenfield environment under the direction of VolkerWessels Telecom, involving telecom incumbent KPN, cable companies Van Gelder Telecom and Allinq and Prysmian.
Telecom specialist Allinq’s field lab proved the perfect location for testing. Rob Walsweer, Project Manager Innovation & Development at Allinq Labs says: "We were very interested in testing these thinner cables and tubes made of 90% recycled plastic. I designed a 350-metre-long route with trenches and 80 and 90-degree bends. We first laid traditional cabling and then compared it with the new system."
Erik: “We saw that Traditional cabling with its thicker, less flexible jacket needed much more room than the newer thinner cables, which could very closely follow the contours of the duct. Following the positive results of these initial tests, KPN initiated the first real-life pilot projects: 2,000 connections in Buitenpost (Friesland) and 9,000 connections in Nijmegen-Dukenburg. As each reel accommodates more cabling, six fewer trucks were needed to deliver the materials for the 11,000 trial connections. Where previously it took four men 20 minutes to install 350 metres, now it takes three men eight minutes. Given the fact that there is a general shortage of technical staff, that’s particularly convenient.”
“The tests demonstrated that Ecoslim makes the realisation of fibre optic networks much more efficient in almost all process steps. The concept was shown to be applicable for all designs and network topologies without requiring changes to the design process. Existing conduits can be used more extensively, avoiding civil works, which means lower costs and less traffic hindrance. Combined savings from operations, material, avoiding civil works and greater installation efficiency amounted to almost €30 euro per customer connection (usually around €65 per connection, depending on delivery agreement. Improved blowing characteristics meant that cables could be placed in ducts up to three times faster. Improved ease of installation also means less - costly - rework.”
At the end of 2020, the concept was fully accepted at KPN. Joost Steltenpool, responsible for KPN’s fibre-optic network: “Together with partners we are investigating how we can install fibre optics faster, more sustainably and with less inconvenience. Our ambition is not only to provide superfast internet to as many people as possible, we also want to do that in a sustainable way. Our customers want that too. This new development is another step in that direction.”
"This is a wonderful innovation from Prysmian, which KPN has put to excellent use, enabling us to pioneer collectively as an industry. That is really powerful. This approach may well become the new standard!”
Rob Walsweer
Project Manager Innovation & Development at Allinq Labs
“Ecoslim is greener, easier to use, more cost-effective… this innovation allows companies to meet their environmental targets without making any compromises whatsoever!”
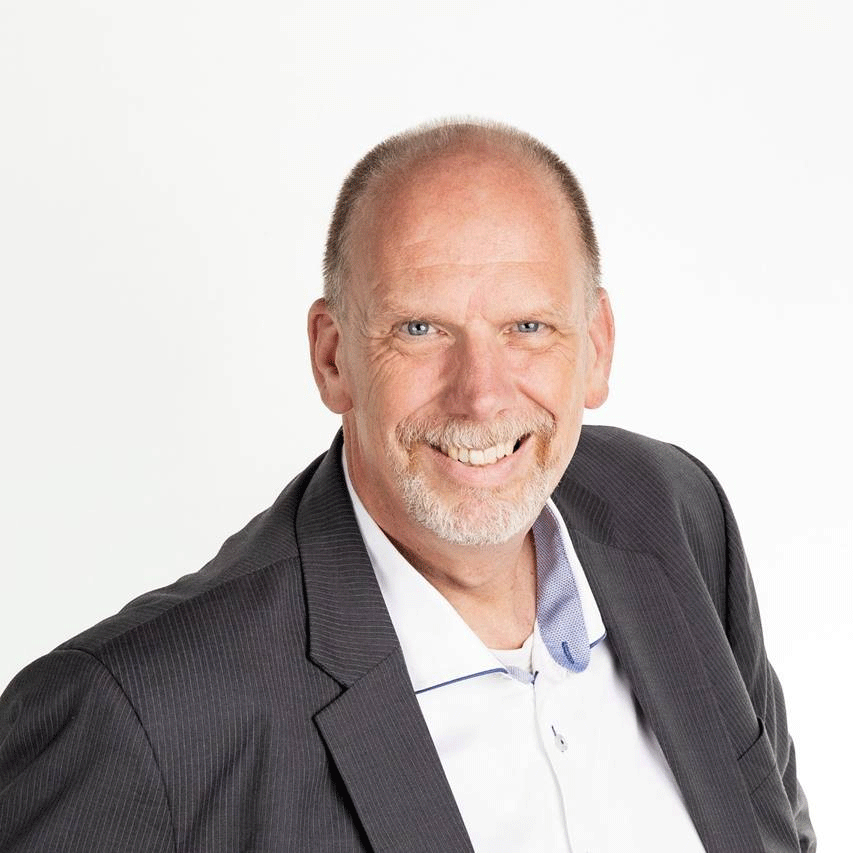
Erik van den Oever
Prysmian Group’s Commercial director Telecom Benelux
The Ecoslim Concept: reduce costs and improve installation time, TCO and sustainability by introducing 4.5 mm 96 fibre cable.
Proven reduction in trenching, especially near CO with high volumes of ducts. Direct savings on material (mainly ducts) 3-4%. Smaller duct diameter increased length per drum.
- Drum reduction > 60%
- Reduced delivery transports
- Reduced warehouse capacity (M2)
- Reduced cutting losses up to 4%
- Reduced movements at the work site