The future is closer than you think
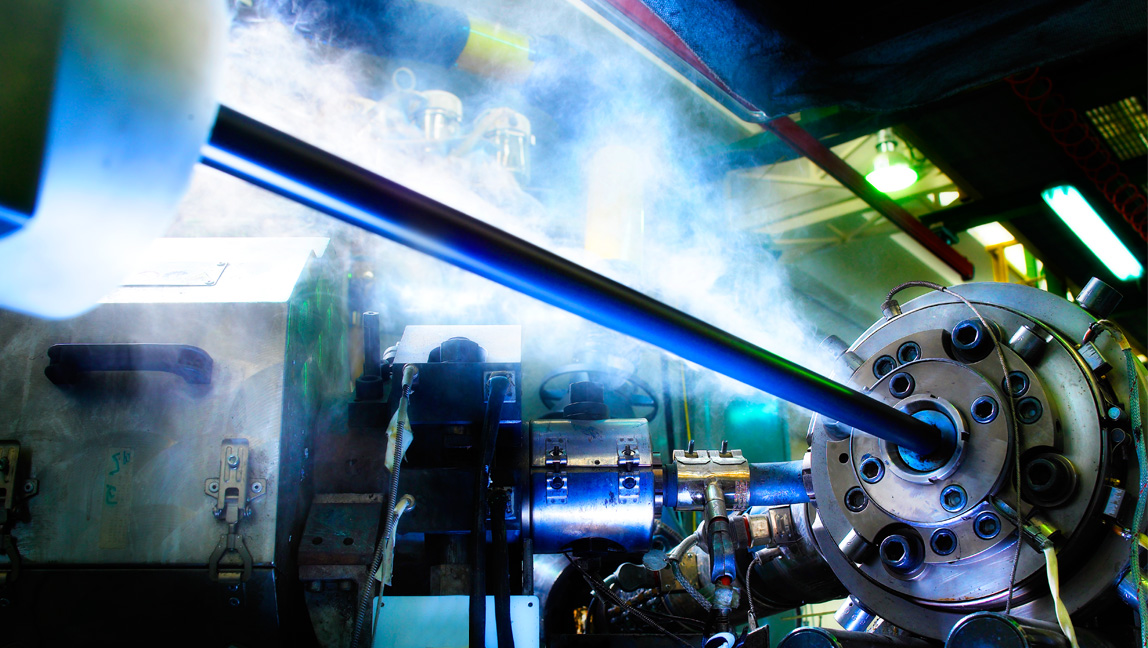
Interview with Marcelo Andrade, SVP Research & Development
FEBRUARY 2017
(Adapted from an original interview with Fabio Sottocornola for Corriere Innovazione)
In the future, distant worlds will become close, joined by enormous tubes, optical and copper cables, and connection systems so extensive they reach right inside our homes.
Tomorrow’s cars will be fitted with onboard optical fibre, far lighter than traditional electrical systems. Submarine cables that carry energy from one continent to another will be more powerful and high performing. Offshore platforms for gas and oil extraction will disappear, replaced by safer undersea factories that are controlled by workers from a distance.
Thanks in no small part to Prysmian, these future scenarios may be closer to becoming a reality than people realise. Today, the company (formerly part of the Pirelli Group) has almost 100 production plants worldwide. But the heart of its research and development capabilities remain in Biccoca, Milan. This former industrial district that has been converted into a technology and service-sector complex that incorporates a university.
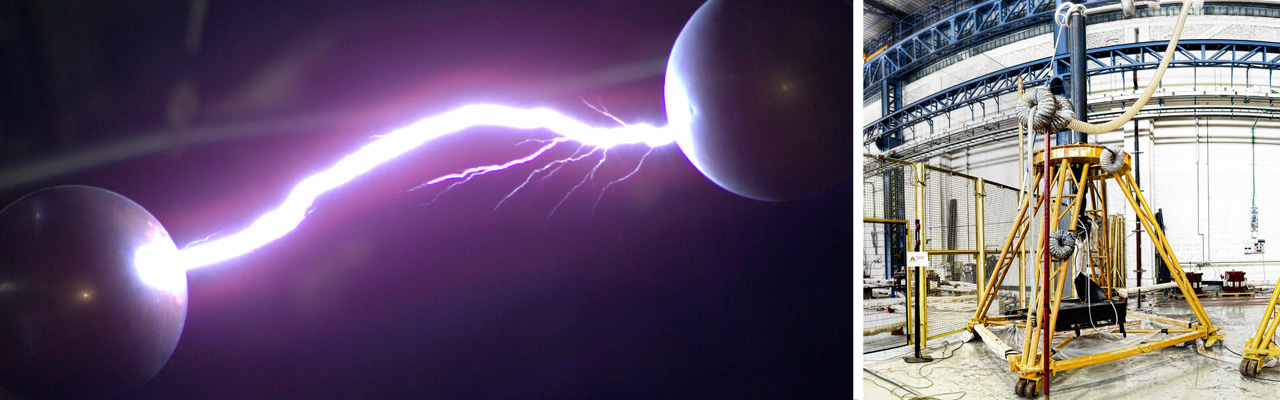
Marcelo De Araujo Andrade, an innovator and a dreamer, who nevertheless has his feet planted firmly in business, Andrade continues, “We listen to our customers’ demand and try to meet their needs.” Developing this technology can be intensely problematic. The laws of nature must be considered and various industry regulations can prove limiting. Connecting continents such as Europe and Africa with new high-voltage submarine cables, or the transfer of enormous amounts of data for telecommunications are just a few of the challenges facing companies. Geographically vast expanses of sea that can reach up to 3,000 metres in depth are also currently too much for existing cable projects to tackle (1,600 metres is the most possible at this time).
But the leading world energy players are determined to tackle those depths. “They ask us, ‘Do you have the technology to make such a cable?’ It is a challenge. The system has to be designed, a more highly performing product produced (perhaps without steel and using composite materials) otherwise it is not technically possible to lay it on the seabed, where it has to last for at least 40 years. Fortunately,” comments Andrade, “we like a challenge.”
Another future scenario sees carmakers who build electric vehicles needing lighter cars in order to fit heavier batteries. “We are thinking about how to pass more power through the fibres to supply the electrical circuits, thereby replacing copper or aluminium cables with optical fibre, which at the moment is only capable of switching headlights on or off, but cannot support the necessary power supply,” says Andrade.
New materials present another test, starting with the graphene used in certain compounds. How can it be used? “We still do not know precisely, we are studying it. It seems interesting as a barrier against liquids entering the cables, but we have to understand how much it costs, and how much to actually put in the compounds.” There is also ethanol current used to ensure eco-sustainable products. Or carbon nanotubes, a sort of spun yarn that is an efficient conductor and weighs five times less than copper, with the added benefit of having greater electrical and chemical performance. Flexible and light, it appears ideal for applications such as elevators, aviation and our homes. “We are just starting to study these new materials”, recounts the engineer. Including one he jokingly calls ‘the chilli pepper’ – a truly innovative core that will be added to the common polypropylene base.
Research processes for the ideal product are carried out in the heart of Prysmian’s Milanese laboratories. Everything from the chemical solution, to the colour and the rubbery prototype will be produced before undergoing an impressive number of ‘tortures’ - a thermal cycle that simulates ageing and tests resistance to fire and chemical attacks, strain, corrosion and impact.
Then come another round of seemingly endless tests: a new-generation scanning electron microscope allows the molecular composition of the materials to be analysed whilst electrical test building is dominated by enormous towers that produce current with up to 2.4 million volts. It takes more than a year to go from order to certified product.
“Here we are developing products using materials and technologies that do not have a market yet, but for which we believe a market will exist in five or ten years”
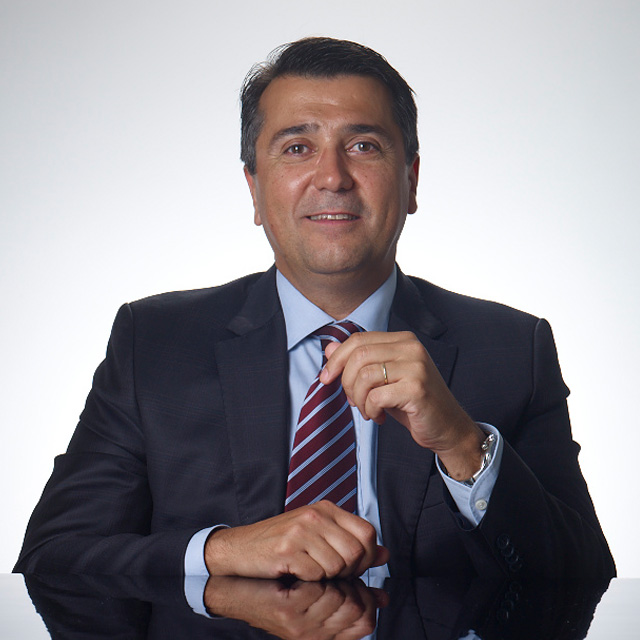
Marcelo Andrade
SVP Research & Development
And let’s not forget optical fibre, for which Prysmian is one of top manufacturers, producing around 30 million kilometres yearly worldwide. “We are working to reduce the size and expand fibre density per square millimetre,” explains Andrade, who foresees scenarios with enormous potential for TLC transmissions via optical fibre.
Today, the most exciting challenge for this engineer with a passion for the sea concerns offshore drilling platforms, where people risk their lives daily. “There are designers and scientists who are convinced that the oil and gas world must go downwards. Down into subsea factories – installations as large as Milan’s San Siro Stadium completely underwater. Human control will take place on the mainland, perhaps at a distance of 300 kilometres. A cable network will be required to manage these structures. We have no idea about costs, but our company will follow and help to shape these trends.”
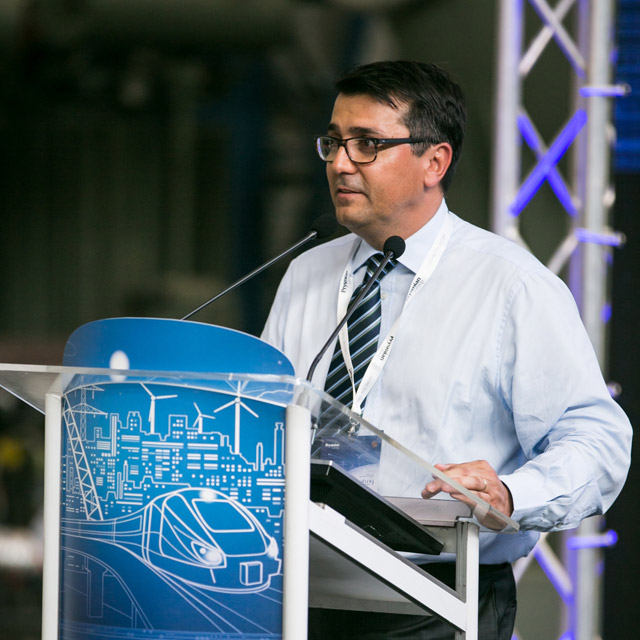
Chi è Marcelo Andrade?
Brasiliano, laureato in Ingegneria meccanica, Marcelo de Araujo Andrade lavora per Prysmian fin dall’inizio della sua carriera. Dal 2012 è responsabile della divisione ricerca e sviluppo, che conta 550 dipendenti.
/ Key Facts
30 million kilometres | The optical fibre produced by Prysmian yearly.
The chilli pepper | A truly innovative core that will be added to the common polypropylene cable bases.
Underwater drilling | Deep oil and gas extraction will be controlled remotely in the future.
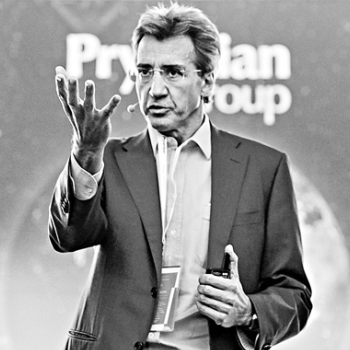
MAKE IT PROGRAM
Make It: Good people make great companies
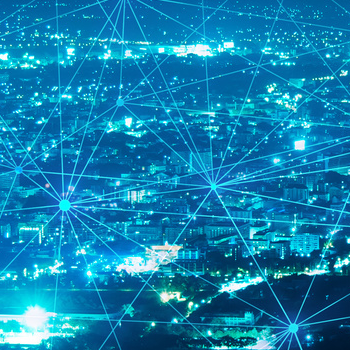
CORPORATE
Prysmian reinforces its digital presence
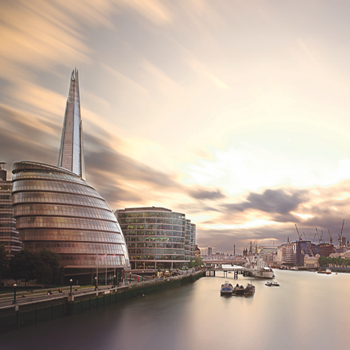
CORPORATE
Staying the course, in the UK
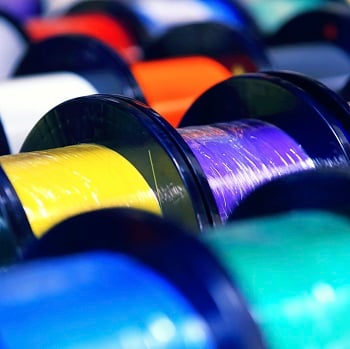
FAST TRACK PROJECT
The future starts in Calais, Prysmian’s first 4.0 factory
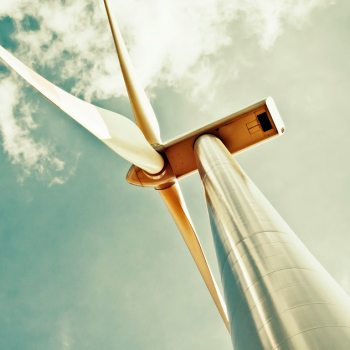
POWER GRIDS
Prysmian joins Tesla’s renewables challenge
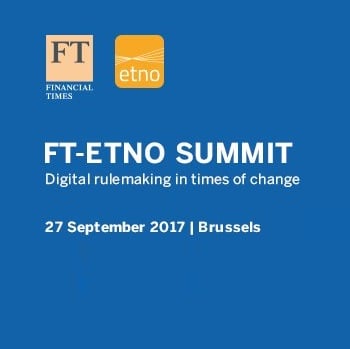
FT-ETNO SUMMIT 2017
Debating the connectivity of tomorrow
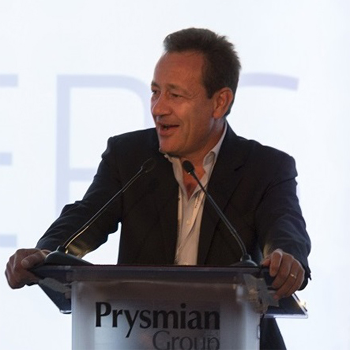
GRADUATE PROGRAM
Prysmian CEO welcomes 50 young hired
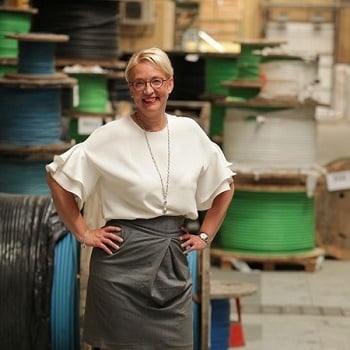
PEOPLE