Keeping Prysmian Group’s supply chain operations on track during coronavirus epidemic
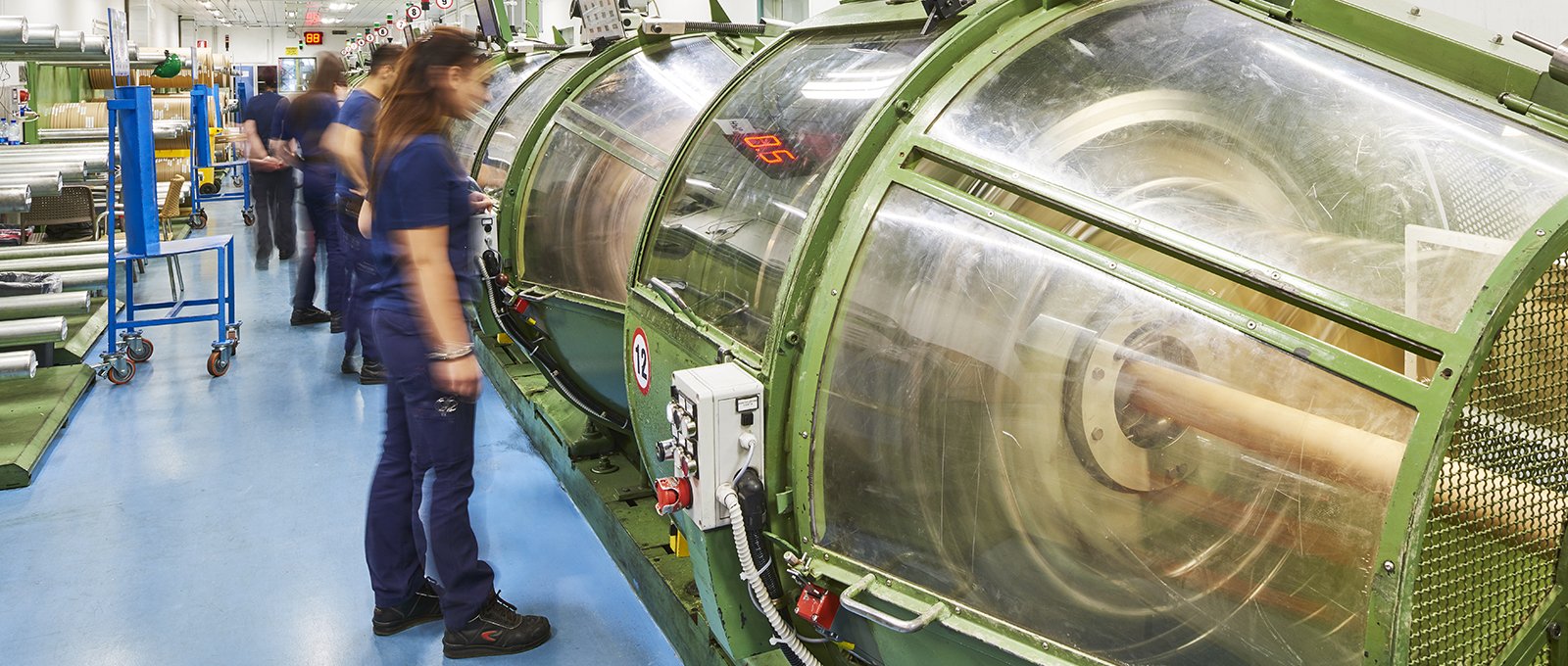
Prysmian Group supplying 600,000 masks to factories each month
“I’m not going,” the executive said. “There is some sort of strange flu epidemic there.”
Pirondini agreed it was better not to take the risk. On January 4 the BBC had reported a “mystery virus probed in Wuhan.”

“I realized just how serious it was after this decision made me start watching the numbers coming out of Wuhan and the steps the government was taking, and it didn’t add up – the steps were a lot worse than the numbers called for. Our 1,000 employees in China lived through a very serious lockdown. And this gave us a small head start with operations for the rest of the world.”
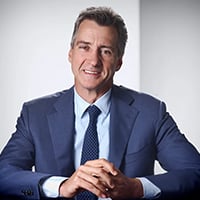
Andrea Pirondini
Chief Operating Officer
An early start was key
That early head start means that headquarters was kept nearly free of contagion; Prysmian’s factory workers have been supplied with 600,000 masks per month as of mid-April; and that all key supply lines are under control, said Pirondini.
While the shift to smart working at Milan was relatively straightforward, making sure production continued where possible while keeping Prysmian’s 22,000 industrial workers safe in plants around the world required teamwork, constant communication, and flexibility. Not every government ordered plant closures, since Prysmian has been considered an “essential industry” in some countries because of its role in supporting energy utilities and telecoms operators to ward off any risk of blackouts or glitches.
“You can’t implement emergency health measures at 100 factories by sending out a memo,” he said.
Orders still being filled
We have tremendous support from the Prysmian organization in the various regions. Along with safety for staff and workers, we have two other priorities in terms of operations: controlling cash flow, and supporting clients. Orders are being filled with a minimum of delays, or sometimes no delay at all, Pirondini said, because Prysmian’s global supply chain and presence across five continents means “we manage our factories in cluster in terms of different clients and product types, and this helps us reallocate and meet client demand.”
Demand has slowed for some of Prysmian’s cables products, and picked up for others. Orders in the energy distribution sector have not seen strong slowdowns, he said. The telecoms sector demand has actually slightly accelerated because of extraordinary maintenance to the network -- which has become a vital asset for work and families in the U.S. and Europe during the lockdown. The construction sector is at a standstill.
“You have to monitor transport every day to find a solution,” he said. “And we have.”
For the Operations staff, staying on top of the health emergency has called for dealing with new demands that go far beyond smart working.
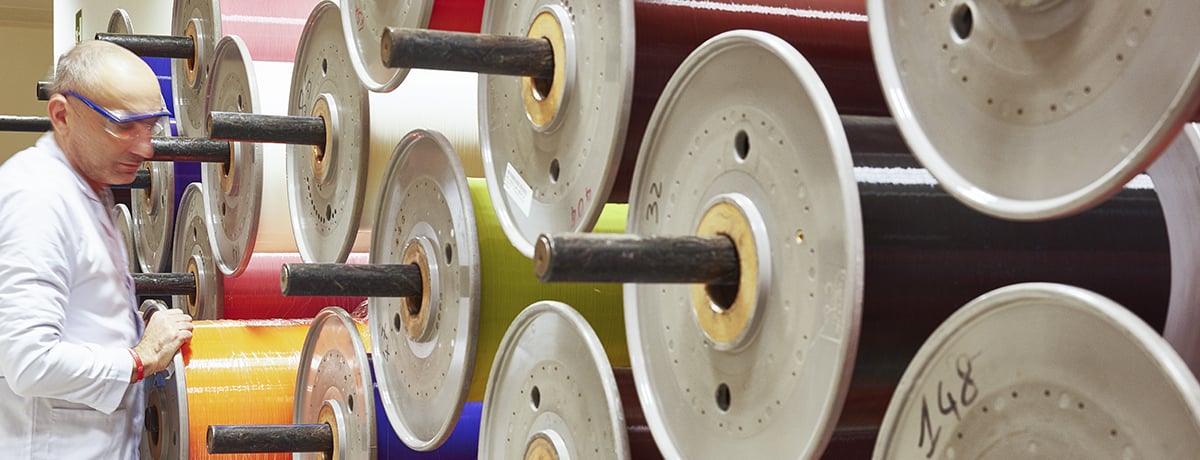
“The picture changes continually, and we are learning to adopt a sort of high-frequency synchronicity in terms of planning. We are reasoning in terms of various scenarios rather than classic monthly, quarterly and yearly plans and most of all continuously adapting to an ever changing set of things”.
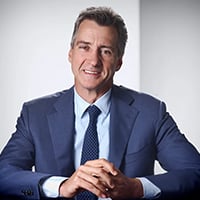
Andrea Pirondini
Chief Operating Officer