Prysmian successfully rolls out submarine interconnection project for Greek islands
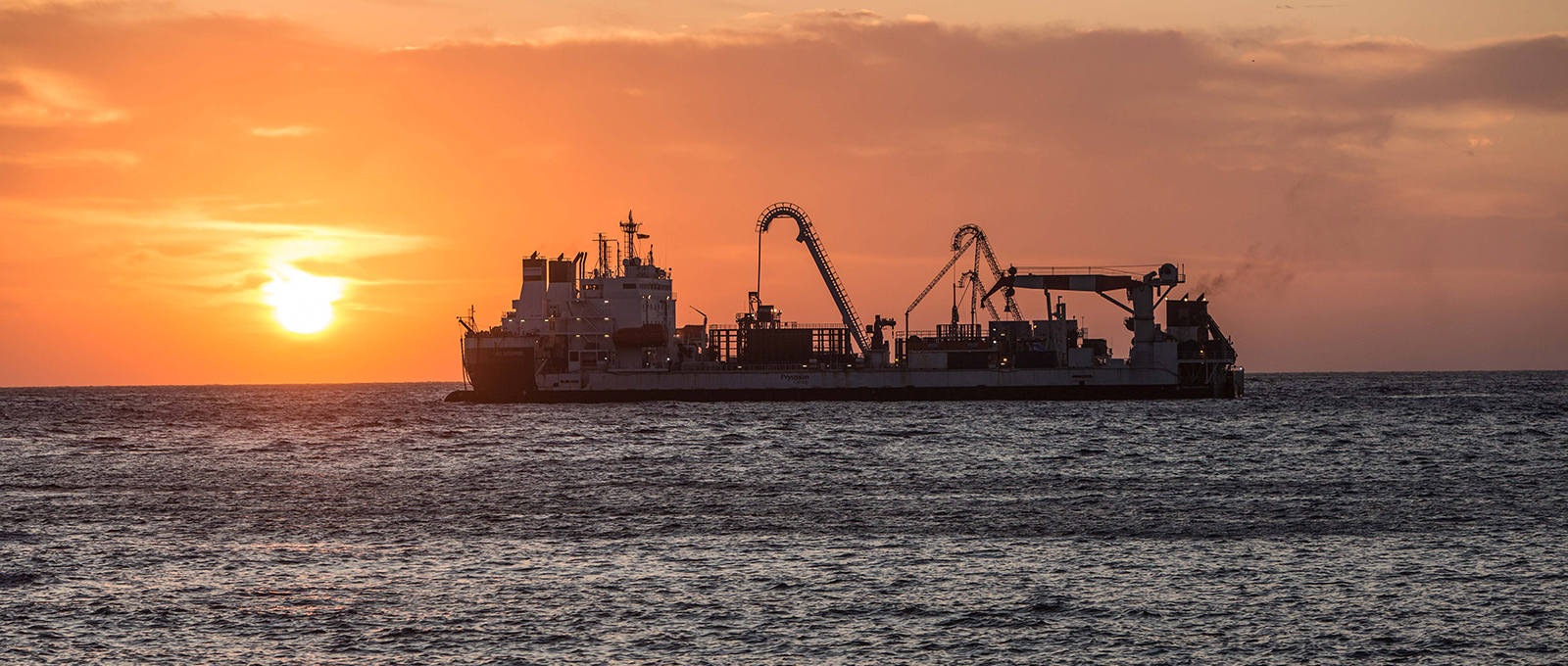
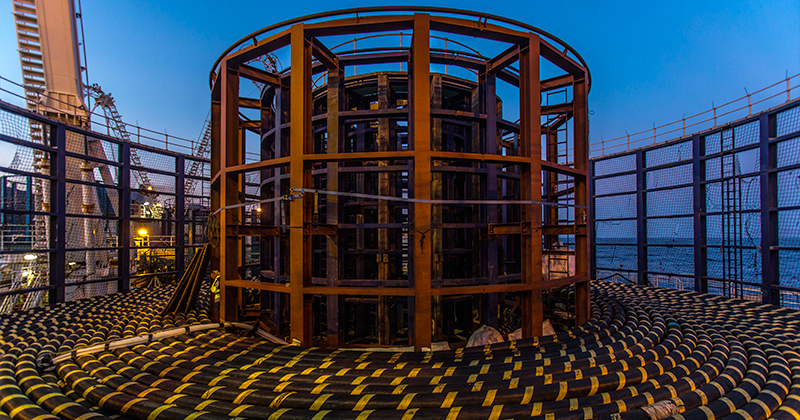
This project involved the design, supply and installation, and related land civil work for two turnkey High Voltage Alternating Current (HVAC) cable systems. These consist of 150 kV three-core cables with XLPE insulation and double wire armouring, along with two fibre optic cable systems.
For this project, the Group developed, supplied and installed the world’s first non-metallic armoured cable, designed with a composite material based on High Modulus Synthetic Fibre. The synthetic armour may be up to 30% lighter than steel.
"When we speak of ‘high modulus synthetic fibres’, we’re usually referring to a family of different fibre materials, characterized by an improved ratio between modulus and weight, when compared to steel. In the case of Evia, one particular synthetic fibre was used. An extensive optimization and testing program, including long environmental compatibility tests, was carried out, in addition to all testing necessary to qualify the system’s mechanical and electrical characteristics."
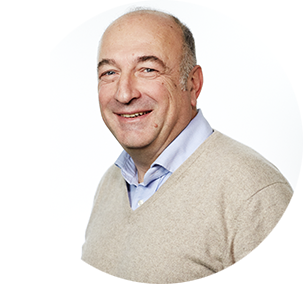
Stefano Franchi Bononi
R&D Projects Director
“We used a new three-core AC cable design concept for the Evia-Andros-Tinos project, because it offers reduced weight while maintaining the bending and longitudinal load characteristics required for installation at great depth”, explains Giovanni Leonardo Curtotti, Director Mediterranean Region Project Management with Project BU.
“Maximum water depth between the islands Evia and Andros is around 550m. This approach allowed us to design a cable suitable that can be installed at depths of up to 1,000m. The innovative cable technology will indeed be used in 2020 for the Crete-Peloponnese submarine interconnection project, which requires an installation depth of about 1,000 m, allowing a strong reduction in installation risks compared with metallic armoured cables. These technology solutions even allow us to reach installation depths in excess of 3,000m, as confirmed by extensive internal tests. Mechanical performance and environmental compatibility have also been fully assessed with our internal testing programs.” Because the cable allows ultra-deep installations, customers may take just about any submarine cable route they need. Stefano: “If you can lay cable at 3,000m, clients can choose whatever route they want.”
Today’s submarine cable market is demanding lighter weight, higher power transport capacity, reduced losses and enhanced sustainability. Land and submarine cables need to be recyclable and use less and less metals. Synthetic fibre has been in use in business areas such as Telecom and energy cabling for sometimes. As a result Prysmian was able to leverage existing know-how to develop the new submarine application, and carry out the previously mentioned assessments in terms of environmental compatibility, design and mechanical/electrical testing. Submarine cables were manufactured at Prysmian’s Arco Felice (Naples) centre of technological and manufacturing excellence, while land cables were produced in Pignataro (Naples). Marine cable laying activities are performed by the Group’s ‘Cable Enterprise’ cable-laying vessel.
Track record
Prysmian has a long-standing track record in the development of submarine interconnection milestone projects in the entire Mediterranean region, such as Italy-Greece, Sardinia-Italian Peninsula (SA.PE.I.), two interconnections between Spain and Morocco, two projects in the Balearic islands (Spanish mainland to Majorca and Ibiza to Majorca), Capri-Torre Annunziata and Capri-Sorrento in Italy and the Dardanelles link in Turkey. This project is one of three submarine power interconnection contracts that IPTO has awarded Prysmian Group in Greece, following the Lavrio-Syros HVAC interconnection of around 105 km and maximum water depth of 330m and preceding the Crete-Peloponnese interconnection mentioned above.
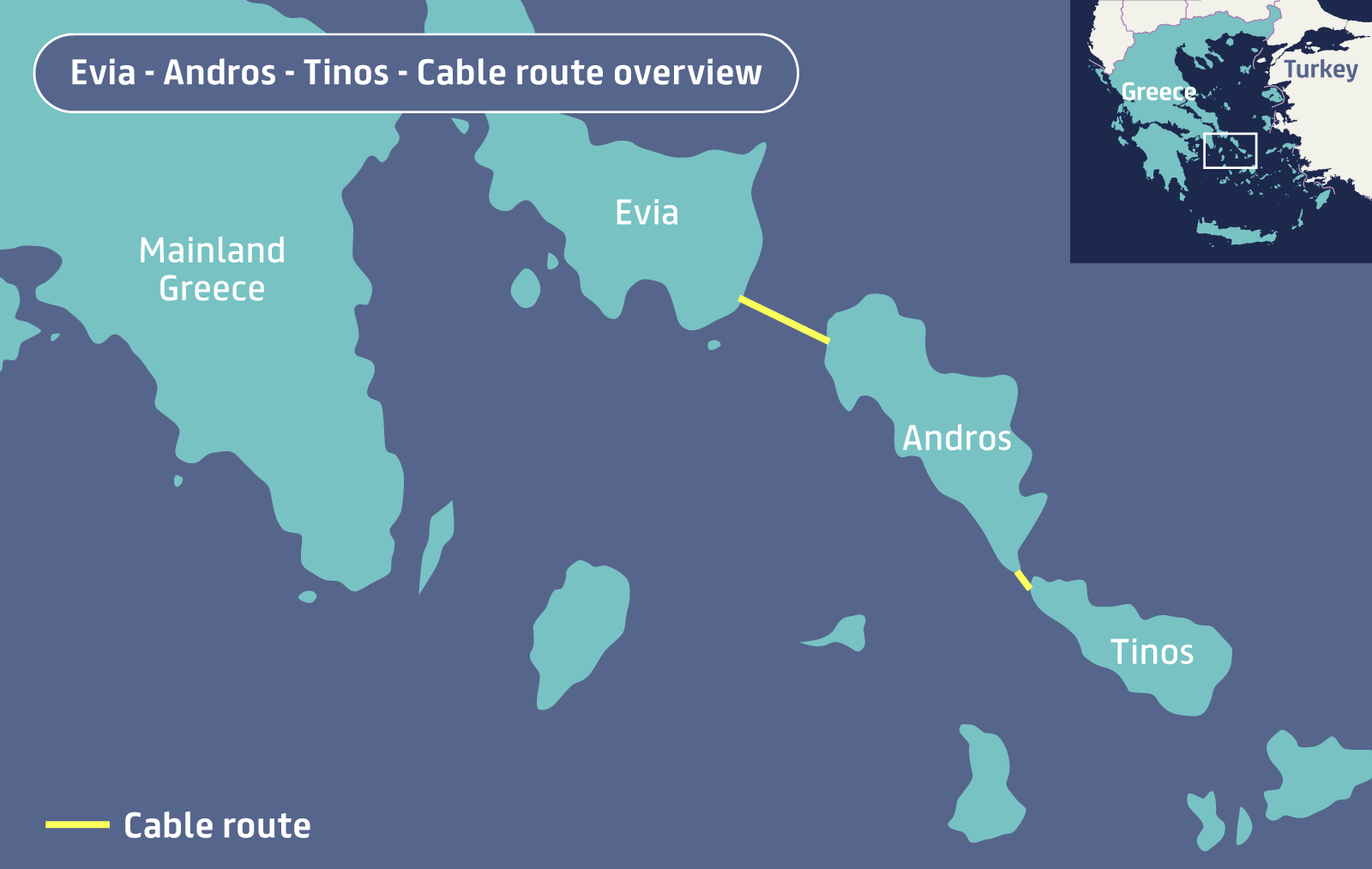