Aluminium is well known for being light, strong, conductive and above all, for its infinite recycling potential. This has made aluminium a fundamental material across many industries, including in electrical cables. However, there is a down-side – it can be extremely energy-intensive. As aluminium is not found in a pure state in nature, it has to be produced, and this is mainly achieved through the electrolysis of alumina (aluminium oxide), a process that, in addition to generating CO2 during the process, requires large amounts of electricity. To produce this energy, in the absence of a supply from renewable sources, significant greenhouse gas emissions are generated, making aluminium an industrial process that contributes to 2% of the total man-made emissions produced worldwide.
Aluminium is a large contributor to carbon emissions worldwide. Can low carbon aluminium help drive down the impact?
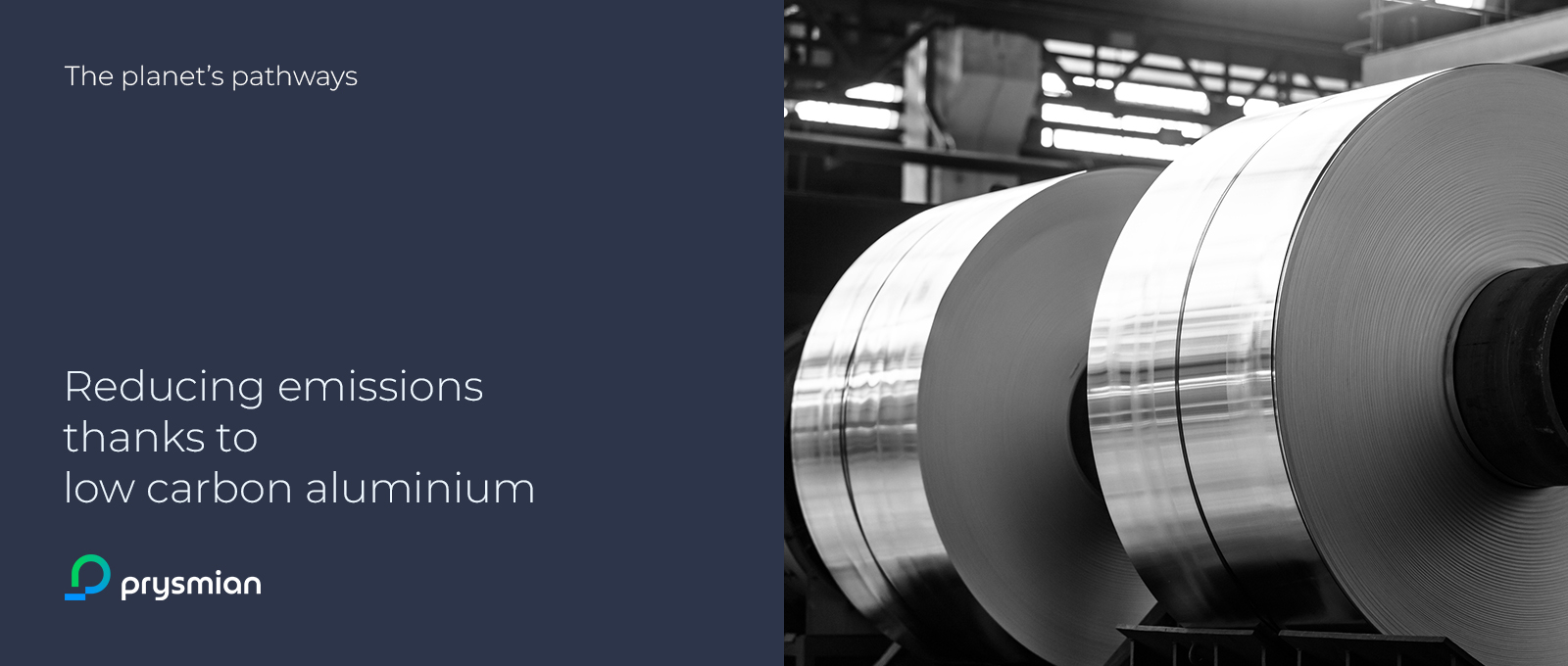
The impact of aluminium on global warming
At present, the aluminium production process is not compatible with the goal of limiting global warming to within the threshold of 1.5° by 2030, as envisaged by the Paris Agreement. To achieve this, the aluminium industry needs to reduce its emissions from the current 16 tonnes of CO2 per tonne of aluminium produced to less than 0.5 tonnes of CO2 per tonne of aluminium by 2050. Not an easy challenge.
With the urgent need to address climate change and meet global decarbonization goals, the aluminium industry has embarked on a path towards more sustainable production with initiatives aimed at drastically reducing the emissions associated with the creation of this metal.
Prysmian's commitment to reducing emissions
Prysmian, aware of the importance of aluminium for its business and its impact on the climate, is committed to taking clear measures to reduce the emissions associated with the production of this metal.
Currently, Prysmian is one of the largest buyers of Europe's low carbon aluminium thanks to its relationships with producers:
- More than 50% of the aluminium volumes purchased by Prysmian come from suppliers that use renewable energy, as a result limiting Scope 2 emissions.
- During 2023, six Prysmian plants used 100% low-carbon aluminium: Delft, Arco Felice, Amfreville, Gron, Sicable, Wrexham.
Prysmian also recently entered into a five-year partnership with Rio Tinto, a supplier of low-carbon aluminium that is produced using hydroelectric energy. This agreement is in line with Prysmian's goal of becoming carbon neutral by 2050.
The innovation behind reducing the impact of Aluminium
The carbon footprint of aluminium is linked to two main contributions: electricity for the process (Scope 2) and direct emissions, especially during the electrolysis phase (Scope 1).
To reduce the environmental impact, there are initiatives aimed at reducing the contribution of these two components. In the Aluminium Sector Greenhouse Gas Pathways to 2050, International Aluminium report, 3 main ones have been identified:
Scope 2: Decarbonization of electricity
As explained above, the smelting of alumina into aluminium requires a lot of electricity, often produced by coal or natural gas power plants. This means that almost 60% of the total CO2 emissions produced by the aluminium sector (amounting to around 1.1 billion tonnes per year) come from the production of electricity consumed during this process.
The use of renewable energy as a source for the electrolysis process is the key to eliminating the contribution related to this.
When we refer to " low carbon aluminium " in the market, we normally refer to production cycles that use renewable energy and are therefore able to achieve a carbon footprint < 4 tons of CO2 / ton of Al (Scope 1 & 2)
Scope 1: Reduction of direct emissions in the electrolysis phase
Direct emissions are a significant source and at the same time – with the technologies available until yesterday – unavoidable: the electrolysis process of aluminium production uses graphite anodes in which the carbon of the anode combines with the oxygen of the alumina, giving rise to carbon dioxide on one side and metallic aluminium on the other.
To address this contribution, the research followed two main streams:
- On the one hand, the development of inert anodes for the electrolysis of aluminium without the use of carbon. This technology represents a real revolution in the sector and is in the process of industrialization.
- On the other hand, carbon dioxide capture and storage projects that seem to be technologies that are not yet mature for efficient large-scale use for these applications.
Scope 1, 2 & 3: Recycling and Resource Efficiency
Making collection rates more efficient and optimizing resource efficiency by 2050 would reduce the need for primary aluminium by 20%, consequently reducing emissions from the sector (estimated reduction of 300 million tons of CO2e per year).
Transition to aluminium low-carbon, a collective effort
Low-carbon aluminium is an indispensable solution to achieve global decarbonisation goals and to combat climate change. With the adoption of renewable sources, in the near future with innovative processes such as inert anode, it is possible to drastically reduce the CO2 emissions associated with the production of this metal, without compromising its quality or performance. Instead, an inert anode is an electrical conductor that does not undergo oxidation or reduction, thus preventing the formation of CO2 and helping to reduce greenhouse gas emissions through the production of pure oxygen in aluminium production plants.
Prysmian is aware of the challenge and responsibility that this involves and is actively committed to using more and more low-carbon aluminium for its operations. But the transition to a more sustainable model requires the commitment of all stakeholders involved: manufacturers, suppliers, customers and policymakers.