Cross borders electrical connections, interconnector and export cables, are increasing in length and have longer lifetimes, making the need for proper maintenance and fast repairs to end outages more urgent than ever.
Prysmian Comprehensive Solutions to navigate the unforeseeable
Asset monitoring preventive maintenance ready to take action
Asset monitoring
Toggle Details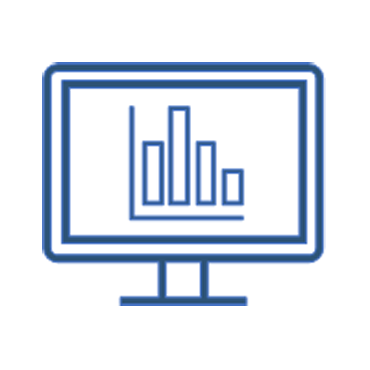
Prysmian’s IMR services can be split into three main areas that can fully cover the operation and maintenance needs. Firstly, there is the asset monitoring. The company, through EOSS (Electronics and Optical Sensing Solutions) installs cutting-edge sensors in the cables to measure factors such as the temperature, the acoustics and partial discharges, microscopic phenomena that signal that an electrical system is deteriorating. Prysmian can provide 24/7 monitoring of such Data on behalf of its Clients to provide quick responses, diagnostics and analysis based on long lasting experience and expertise.
Preventive maintenance
Toggle Details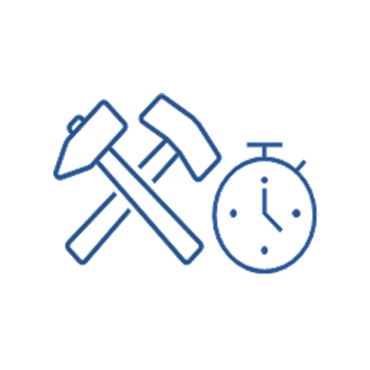
Secondly, it provides preventive maintenance such as inspection of the cable routes, to check the condition of the installation. Currents and waves can mobilize the sea bottom and expose part of the cable, and a periodical survey can identify if there are areas exposed so they can be reburied. Spare parts management, and periodical inspections of those is also key to ensure critical components are all available, in good condition, and easy to locate and recover in case of need.
Ready to take action
Toggle Details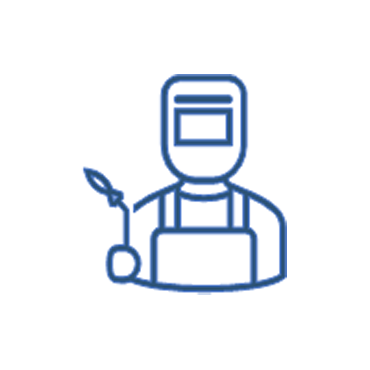
Lastly, there is the repair element, which involves being ready to take action. This includes defining scenarios for situations that could occur and preparing the tailored engineering for specific solutions. It also involves ensuring the availability of skilled staff, with Prysmian being able to leverage one of the biggest pools of highly skilled high voltage cable jointers, as well as preparing the availability of vessels and equipment.